By Rapid 3D Technologies - 3D Printing Service
02/04/2018 Sand casting is a process in which fine moist sand is compacted or rammed around the wood pattern placed in a box-like framework constructed out of wood or metal. At the end of the process, the pattern is removed from the sand which leaves behind a cavity that can be filled with molten metal. The metal cools and then hardens and is removed from the sand. The sand is then able to be recycled. This process also required the extra material to be removed from the finished product and clean-up performed.
Rapid 3D Technologies located at Ganapathy, Coimbatore, India is engaged in working with various foundries to develop such 3D printed patterns using special plastic material.
Before including 3D printing, the industry’s traditional methods include:
1. Labor intensive hand carved wood patterns for impressions
2. Varying inaccuracies due to hand-made parts
3. Multiple patterns to create positive and negative models
By applying 3D printing, the casting process experiences
1. Reduced costs with prototyping and test models
2. Reduced labor with automated printing process
3. Increased accuracy with precision digital models
To begin the process, a 3D model of the component needs to be created using 3D software. Rapid 3D Technologies is also engaged in 3D modeling apart from 3D Printing. This design is then printed as a prototype and installed onto the original hardware to measure fit and tolerances. Along with this feedback and taking into consideration the amount of shrinkage that the metal will experience with cooling, the necessary changes are made in the model until the desired outcome is met
Now that the dimensions are finalized, this will now be used to create a positive and a negative additively manufactured pattern that can be used in the molding process.Post processing techniques are then carried out to improve the surface finish of the patterns.
A ‘core’ is added which will will be used to prevent metal from flowing into the space where a hollow part is required.To complete the cast 3D printed patterns are then used to create the impression into the sand. This will be made in two halves known as cope and drag. One of these two halves will be given a gate for metal to be poured in to. These cope and drag are then joined together using guide pins provided on the edges of the mold boxes to avoid misalignment. Necessary vent hole are provided for the gases to escape during pouring of metal. Finally Metal is poured into the gate and cooled for sometime revealing the desired product.Excess sprue’s and gate are need to be removed and the object will usually require substantial cleaning.
Rapid 3D Technologies - 3D Printing Service
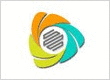
Overflow ActionsUsing Additive Manufacturing Technology we are providing 3D Printing service in Coimbatore - Tamilnadu focusing on Prototyping & Low batch production using 3D printing.We are located at Ganapathy,Coimbatore and are working with many automotive, medical, plastic injection molding …